If you have been following our community for a long time, then you are familiar with the look of the Punto Design outdoor furniture collections. You can find some of the products on our website, but in most cases we work on individual design, taking into account the wishes of customers.
If you have been following our community for a long time, then you are familiar with the look of the Punto Design outdoor furniture collections. You can find some of the products on our website, but in most cases we work on individual design, taking into account the wishes of customers.
We use the most advanced technology and modern equipment in the manufacture of products. Today we will talk about cold stamping method of sheet metal processing
A vivid example of such a product is the “Box” bin. The product, made of galvanized steel with powder coating, will perfectly fit into the look of any public space.
What do we use?

The Shear Genius® SG machine is a unique combination of integrated punching and cutting.
Functions of this cell:
- automatic sheet loading
- punching and cutting functions from the right angle
- automatic sorting of waste and products in various places
Most of the components of the fabricated material are rectangular. The economical method of their production is punching at the beginning, then automatic rough cutting of components with integrated cutting at a right angle. In such a situation, the combination of punching and cutting works as an independent cell or as a central hub with automatic material feed systems at the level of the production cell.
Bene fits:
- Modular design - two alternative working levels and the ability to add automation for flexible material feeding
- More capacity, quality and efficiency
- Material savings - no waste and scraps
- Traces and marks do not remain on the material
- Quick return of investments
- Brush tables for low noise and maintainance of a perfect sheet surface
- Punching force of 30 tons to a depth of 8 mm - various user solutions
- Punch cutting safety tools - fewer strokes. Less wear - faster production and flow of parts.
Environmental friendliness
- PСomplete servo-electric drive - no harmful waste of oil
- POperations can be carried out on the one hand - simple and efficient indoor logistics
- PThe efficiency of the occupied space - 105 sq.m. with sheet loading device
- PServo-electric punching and cutting - low cost of inspection
- PAverage energy consumption: 5 kW = electricity savings
- PMaterial savings - 10% (on average) better sheet recycling compared to purely punching machines
- PNoise level only 73.3 dB with materials 1 mm thick (mild steel
How it works
High forming - servo-drive in the lower frame of the machine raises the molding matrix to the position and provides a force of 200 kN for quick and accurate production of complex shapes up to 16 mm (incl. Sheet thickness).
Quick part identification - a few embedded ready-made solutions for adding information for components that provide reliable identification of different types of marking tools.

Simple and flexible punching - as an option, a servo-controlled tapping station TU6 with 6 taps and a monitoring system is available.
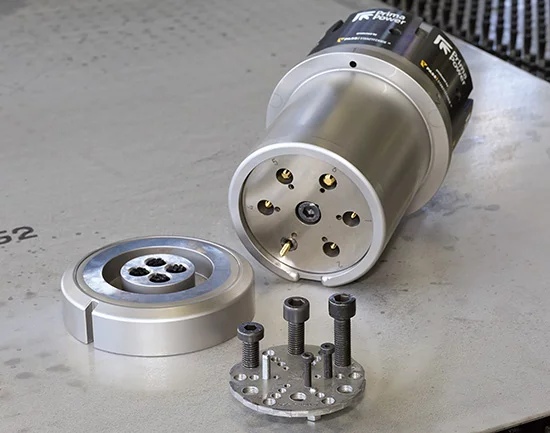